Throughout the ages, silver has long been valued for its unique antibacterial and healing properties. Ancient Romans would drop silver coins into their water to serve as a disinfectant.
And modern-day astronauts are doing something similar – with a silver-based water purification system aboard the International Space Station.
From water purification to wound healing, silver is used in a myriad of ways to help keep us safe from bacteria, fungi and the spread of infections.
A more recent application is the use of silver in protective coatings and paint systems for industrial, commercial, and domestic use. The key problem with most current coating systems is working out how to maintain the effectiveness of the silver additive over the lifetime of the coating.
Our recent experience with Covid-19 and the increased sanitisation requirements in preventing community transfer and keeping ourselves safe makes this a particularly timely area of research.
A lightbulb moment
Based in Wellington, Dr Eldon Tate co-founded Inhibit Coatings after discovering a way to bind silver nanoparticles within polymer resin during his PhD studies.
Eldon had his lightbulb moment researching the application of his technology as a marine coating, to prevent leaching of toxic paint chemicals into the environment.
“Our initial focus was looking at how the technology could be used on boats to reduce release of antifouling biocides into the marine environment.”
“On one particular field trip, we ended up in a seafood processing plant. The frequent cleaning and sanitisation regimes required in food processing facilities means that the active ingredients used in traditional, additive-based antimicrobial floor coatings are easily washed out – often ending up in drains which ultimately lead to the environment where they can destroy sensitive habitats and marine life.”
“Seeing how the processing plant cleaned their floors, we realised that our technology could be used in a completely different way.”
High-performance antimicrobial coatings
Inhibit’s technology differs from other coating systems in that the active ingredient is not an additive. It’s bound to the polymer resin. This means the silver doesn’t wash out and will retain its antimicrobial effectiveness for the lifetime of the coating.
Inhibit’s technology produces high-performance antimicrobial coatings that uses a broad-spectrum silver antimicrobial agent to effectively kill over 650 different types of microorganisms, including E.coli, Salmonella, Norovirus, Campylobacter and Listeria monocytogenes.
“Our coatings have been tested to prove that they offer antibacterial protection with no end point, and antimicrobial protection with no reduction in effectiveness,” explains Eldon. “This means we can include it in paints, coatings and flooring systems for commercial use. It can bind to plastics which makes it suitable for use in nylon injection moulding. And the effectiveness of the technology across the different applications remains consistent.”
Unique testing opportunity
Inhibit’s coatings are primarily designed for commercial use in facilities with high hygiene and sanitisation requirements – particularly food processing, health care and aged-care facilities.
“Our coatings are already in use in food processing facilities around New Zealand. We’ve been getting excellent results from testing – proving that our technology helps prevent the spread of bacteria and contaminants.”
Eldon acknowledges the current Covid-19 pandemic could be very timely for his product as silver has well-known anti-viral properties. “We’re in the process of getting our product tested to see how effective it is for anti-viral protection.”
“Recently we received a $350,000 grant from MBIE’s COVID-19 Innovation Accelerator Fund to develop anti-viral coatings for hospitals and other high-risk areas.”
“Current antimicrobial coatings used on door hardware like push plates and handles generally contain copper, and we know that Covid-19 can last on copper-based coatings for up to 4 hours,” Eldon points out.
“If our testing shows that Inhibit’s technology can reduce that timeframe, or eliminate it completely, then we have a real opportunity to make a positive impact in the fight against Covid-19.”
Scaling up production
Inhibit Coatings recently completed a $1.5million capital raise to scale the technology up to commercial-sized batches, invest in production and resources, and obtain regulatory approvals in the US to open up opportunities in the global market.
NZ Innovation Booster (NZIB) was involved in the recent capital raise, committing $200,000 to the innovative start up.
“We’ll be using the $200k from NZIB, along with the other investment we secured, to protect our IP internationally and to obtain regulatory approvals in the United States to open ourselves up to the global market,” says Eldon. “It’s an expensive but absolutely essential part of our growth.”
An innovative future
Eldon, along with colleagues Dr Emma Wrigglesworth and Josh Stoneham, are continuing to explore the potential applications for their technology.
“Through our partnership with Polymer Group Ltd, we’re proving the technology is scalable for multiple resin systems. We’re going from 5kg to 100kg batch sizes. Next up will be to produce our first tonne!” laughs Eldon.
“Right now, we’re focused on testing and trialling our technology in the health care environment. We’re keen to find out how our technology performs against the transfer of viruses, especially Covid-19.”
“If our coating technology performs as we think it will, it would be a real game changer for hospitals and aged-care facilities. That’s where we see we can have the most impact right now.”
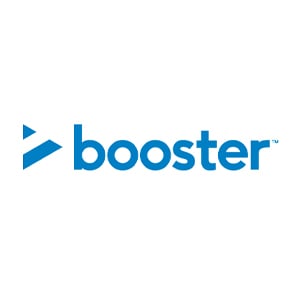